Traditional Warehouse Storage: Staying Organized for Optimal Efficiency
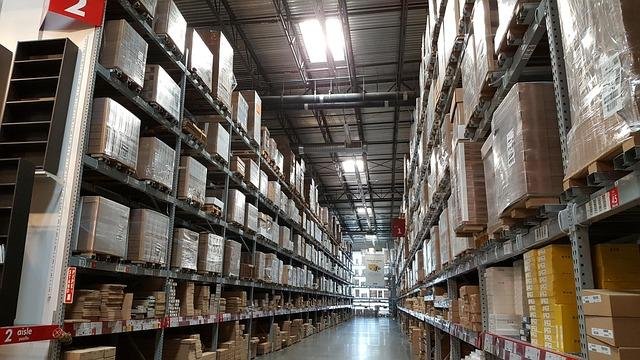
Keeping warehouse storage clutter-free is essential whether you have it long or short-term. That means carefully organizing the space to save frustration from having to sift through a mess when you need to find certain items.
Improperly organizing items can lead to not only difficulty in locating things you need but the potential for damages. Effective storage protects your investments and reduces potential risks.
Simple Ways to Organize Your Warehouse Storage
When you obtain traditional storage, it’s essential to organize the space for maximum benefit and to avoid spending extra for room you may not need. If the warehouse is neat and tidy, the things you need will be readily accessible without digging through piles of clutter.
Creating order is relatively simple with adequate planning and preparation. Consider the following tips when you decide to move your inventoried products to storage for optimal efficiency.
The right size
Select an adequate size for your storage space to avoid paying for room you don’t need. Taking inventory of what you have will help determine the unit you need and planning proper organization for the space will ensure the items are protected while stored.
Maximizing warehouse space improves efficiency and can ultimately save on costs. Businesses can reduce their overhead by maximizing their space, keeping the rent down and decreasing utility expenses.
Reorganize products according to types
Key to optimal warehouse space utilization and design is product organization. If the layout is inconsistent or messy it will take staff longer to perform their duties as they try to find items to complete their tasks. These delays in operations will put schedules behind.
Companies organize products by type and categorize the products setting aside specific areas for the different categories in the space to make it easier and faster for staff to find them. This improves productivity, saving on labor and time. Visit – 8 Essential Tips for Smarter Warehouse Storage – for tips on smarter warehouse storage.
Neat and logical organization
The product organization should be user friendly and consistent. For instance, products can be organized by their name or sorted by manufacturer. This system is easy to understand for all workers when it comes to finding items quickly.
The warehouse should be neat and orderly, meaning the walkways should be clear with no obstacles blocking the path for employees trying to perform their duties.
Not only can this cause delays in handling tasks but it poses safety risks leading to potential accidents or employee injuries. Warehouse equipment should be in its place and storage crates should be closed.
Warehouse vertical space
When the warehouse exceeds its space and you can’t add racks to the right or left, consider expanding upward if there’s adequate room. Making use of vertical space with higher rack that have more levels is an easy way to increase storage capacity.
Before making this move, it’s important to check for stacking restrictions for products above a certain height, including manufacturer storage rack restrictions, OSHA restrictions, and any limits for lift truck vertical height.
You want to avoid storing maximum-weight pallets at your forklift’s extreme upper limit lifting height. This can cause an imbalance and result in the equipment falling.
Excess inventory
Some products fail their projected demand leaving much inventory occupying available warehouse space. The square footage used on excess amounts of failed inventory would be better spent on high priority items that are performing and need the space. Read here for types of warehouse storage systems.
Eliminate the excess inventory enables you to make efficient use of the storage, in turning, helping to save money by not holding on to stock that doesn’t bring a profit in favor of valuable inventory that moves.
In that same vein, there are storage racks in the warehouse that are either underfilled or unused. These should be noted along with the type of products situated near them.
This way you can better plan when new items arrive for better utilization of the space; like items will be organized together for optimal efficiency.
The items that move fast should be conveniently located where employees can readily access them. This will improve workplace efficiency, keeping productivity up, preventing delays and keeping the schedule moving steadily.
Minimize aisle width for maximum storage rack space
Consider making the aisles narrow by moving the storage racks close together to increase storage space within the warehouse. You want to be careful when reducing the width, however, it’s possible for it to become too narrow and create other issues that can lead to accidents or employee injuries.
For instance, the traditional rack systems were designed to accommodate a lift truck which requires a roughly 12 ft width. If the aisles are too narrow for the forklift, it increases risks not only for the staff but also the potential for damaged equipment and to the structure itself.